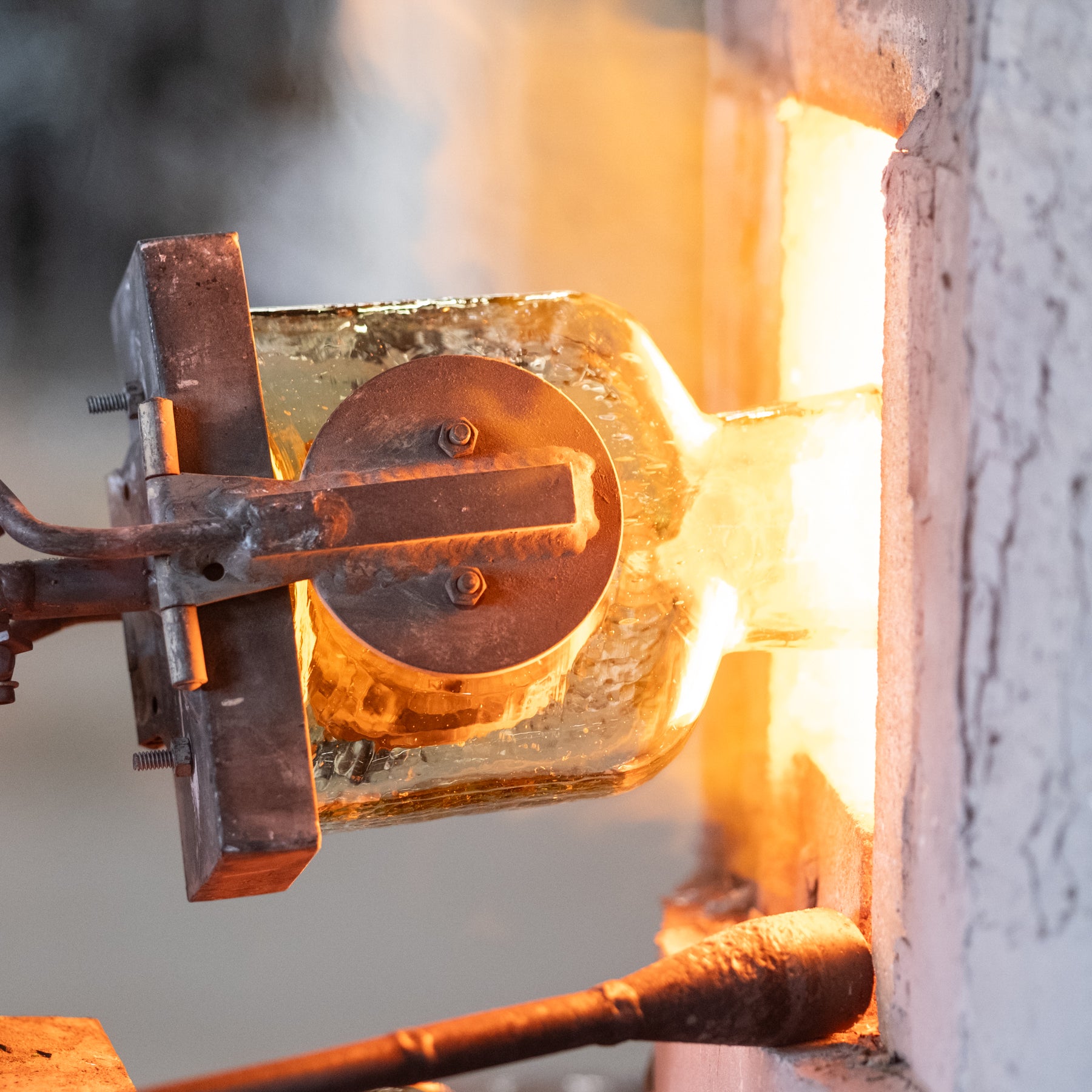
Tools of the Trade Tuesday – The Clapper!
We don’t mean to confuse you, but this is a sticking point for novice collectors of the brand. And our 384 Water Bottle has had enough imitators and copycats over the years to continuously surface this piece as a question mark. But at its inception, this ware was designed to have a flat, punty-less bottom - a feature that has allowed us to make this piece at production speeds to meet perennially astronomical demand.
The ‘clapper’ is a spring-loaded pipe with a flat tray on the end of it. This flat tray is furnished with a piece of heat-resistant plaster. When the Water Bottle is pulled out of its heavy iron mould, the mould-holder pulls it out by its neck and sets in on a box to cool. This is the point in other wares where the piece would be transferred to another blowpipe by virtue of being puntied.
But the mould-holder will place the Water Bottle in the clapper’s flat cradle, and by releasing the mechanism, allow the graphite cookies on either side of the cradle to close around the water bottle’s dimple and hold it in place while the overblow is ground off. Contrary to lore – the clapper does not give the Water Bottle its dimples – but it does use them to its advantage.
The clapper allows the stick up to prop only the spout of the Water Bottle back in the gloryhole while reheating it to pull the ware’s iconic double spouts. The finisher can rotate the piece on the bench in the clapper, which grips the Water Bottle while the finisher cleans up the lip.
The final move with the clapper is to release the spring mechanism and use the carry-in fork to scoop the Water Bottle out and carry it into the Lehr, where it begins its final journey to room temperature at a safe deceleration to ensure the glass cools.
The clapper, historically, was an improvised piece of engineering equipment invented here at the factory - what we often lovingly call our “redneck engineering.” The factory has a long history of inventing needful equipment as new contingencies arise. This is one of the features and factors of glassmaking that makes it such an alchemical wonder to live with and work through: that there are dozens of ways of going about it, each as uniquely evolved to its niches as a Galapagos finch.
We recently partnered with Marshall University’s Center for Advanced Manufacturing and our partner Morgan Smith to reengineer our clapper. We brought it to downtown Huntington to their state of the art facilities, and worked out how its training students and partners might reconstruct this idiosyncratic tool. Morgan his folks deconstructed the piece, scanned it in, modeled it, and then milled and welded the steel to bring us our Clapper 2.0! The changes between our old and new clappers are small, but critical – obviating the need to unnecessarily bend and torque the steel to achieve the opening of the clapper.
You may have tuned out by now, but if you’re the kind of person who enjoys this sort of arcane knowledge – hit us up with your questions! What pieces of glassmaking equipment or process questions do you have? We’re happy to answer those questions – email creative@blenko.com with any such queries!