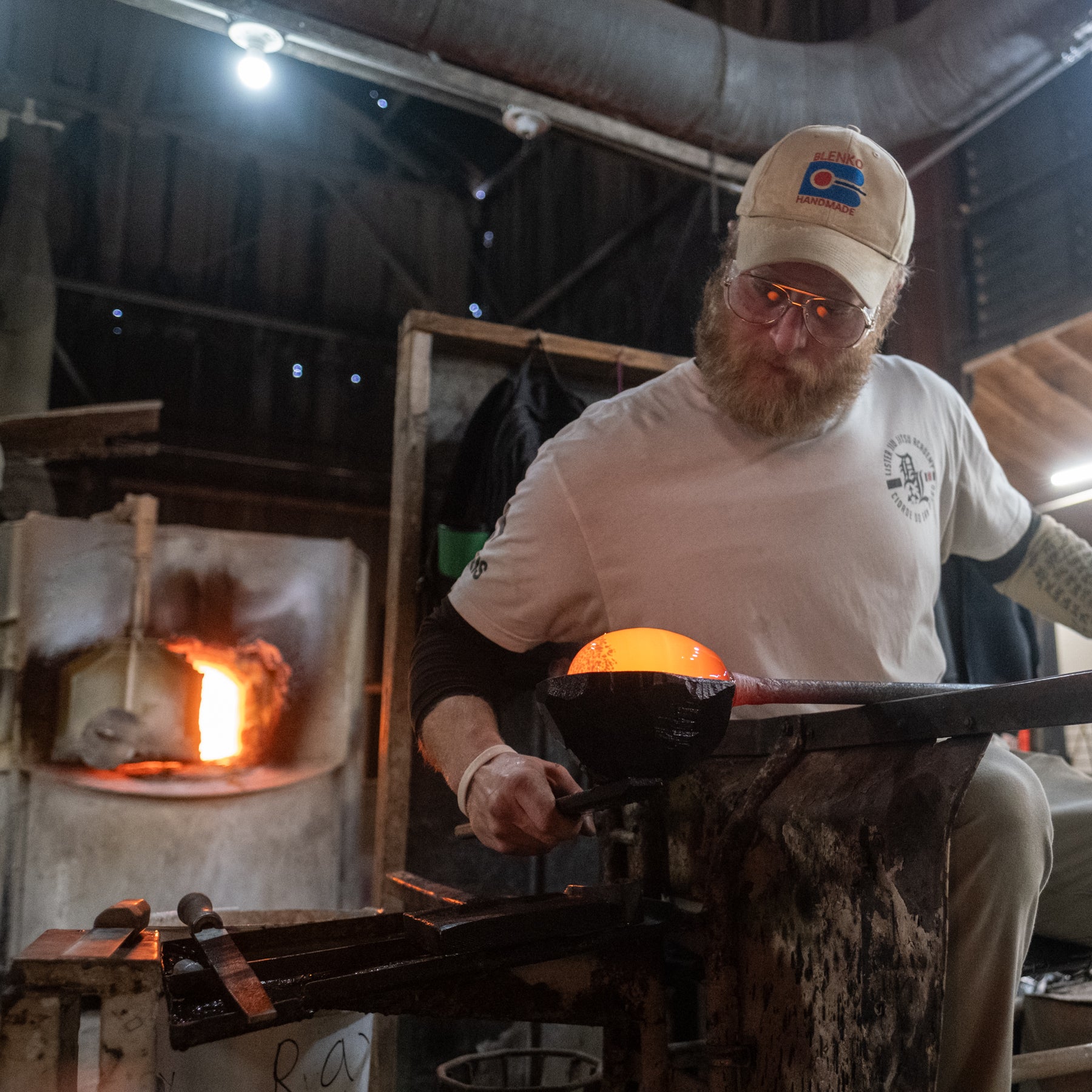
Tools of the Trade Tuesdays – Blocks
Hot glass, you might imagine, is a gooey, viscous, oozy kind of material. When we gather it out of our furnaces, we use centrifugal force on the pipe to keep the hot, drippy glass from dripping hotly off the pipe. So we keep the pipe turning as the glass cools enough to slow down so that we can get it from point A to point B. But even so, when we get the glass out of the furnace, it’s quite literally wound around the pipe.
This is the first instance where blocks come in handy. A gatherer can sit at the glassblowers bench, and roll the pipe along the rails back and forth in front of them. By lifting and rolling the hot glass into the half-cup declivity of the block, the glass is smoothed out, homogenized on the end of the pipe. It’s also helpful in creating a little bit of a ‘shucking’ rim on the bottom of our blown bottles – a hook that allows us to knock the excess glass off of the pipe at the very end of the process.
Why are the blocks in a bucket of water? The blocks are made of the same wood our moulds are made from – cherrywood. As wood will do, if the tool wasn’t wet and soaked through, the 2000-degree glass would burn the tool and create a char that would leave ash on the next piece, and so on and so on. Keeping the block tool wet allows us to use the tool over and over again with only minimal and very gradual burning. The water on the tool also helps cool the glass - and the steam protects the gatherer’s hand from the worst of the heat.
After the glass is reheated from being gathered, the blower will bring the ball back to the bench and block it one last time. This second blocking on the hot glass allows the skilled blower to redistribute the weight of the glass on the end of the pipe through the angle and tilt, and the pressure of the hand holding the blocking tool. For pieces that need - or like – extra glass at the bottom, this is the blower’s chance to push some of the weight of the glass down towards the bottom. This skill is one of the hardest to learn in a skill set that’s already difficult – so it can be an absolute wonder to watch one of our experienced blowers – a Perry Bays or a Ray Adkins, for instance – deftly manipulate the hot glass with the smallest of wrist flicks and pressures.
What’s often most interesting to our customers and our fans is that we make all of these wooden tools on premises ourselves. Our mould-makers pretty constantly refresh these blocks, taking the worn and chipped ones out of rotation, putting some new ones in. A hot shop worker knows they’ve made it when they’ve had a chance to put a brand new block to work on a piece, and the process of breaking in the blocks is a discipline unto itself.
Everything we do at Blenko is by hand - and handmade - so it’s a pleasure to feature the tools that we work with. Because hot glass is a cruel mistress, and too hot too handle, these tools – especially the blocks – are the closest approach we have to laying hands on the forbidden taffy. For most studio artists and beginner glassblowers, blocks are a special tool not to be taken lightly – they take skill to carve and gauge, and because handmade from hardwoods, not cheap. We’re awfully spoiled to make all ours on premises.
In fact, in part because of the cost and the work involved in getting wooden blocks, it’s fairly common practice in most glass studios to do blocking work with soaked and folded newspapers. Creating these panels, paddles, or mitts allows glassblowers to shape the hot glass through paper with their hands - as if clay. But blocks have always suited our production style and our style of glass – and are just the right tool for mould-blowing, specifically.
Check out our cool Coat of Arms suncatcher in Cobalt – our Jenni Gonze designed it to feature some of these very tools of the trade, including the beautiful, hand-hewn blocks!