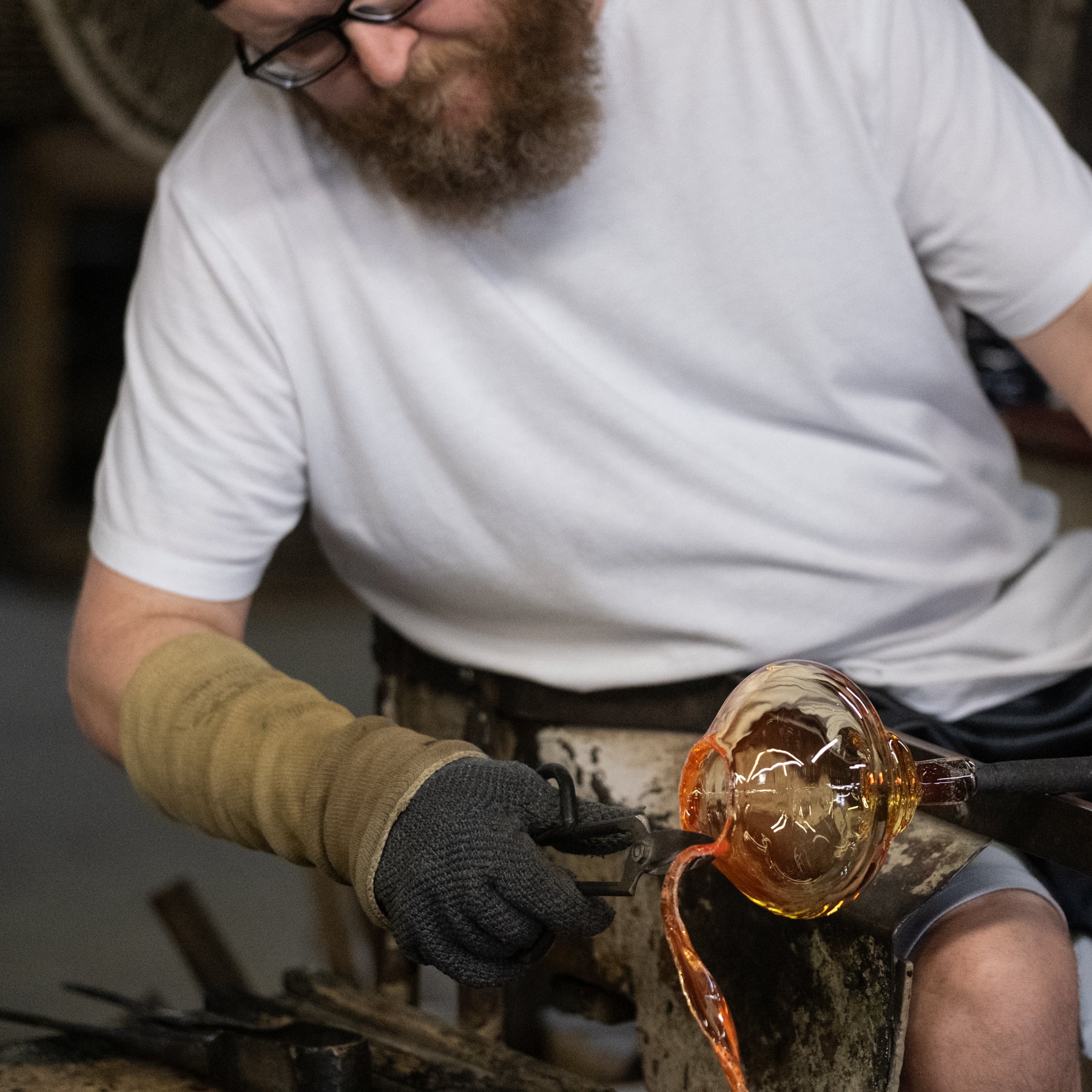
Tools of the Trade Tuesday - Shear Madness!
There are a couple of kinds of heavy iron shears on the finisher’s bench – and it’s the finisher’s bench they mostly live at. The finisher is the second-to-last step in our glassmaking process. By the time the glass comes to the finisher, it’s been gathered out of the furnace, blocked and marvered, puffed into and blown into the mould, and the stick-up’s taken it back to the furnace to reheat it. The finisher comes in at the end of the process and puts all of the - well - finishing touches on the piece.
The first and most important step is trimming the glass. When the glass is knocked off of the original blowpipe onto the stick-up’s punty, it leaves a jagged, sharp, erratic edge on the lip of the piece. The stick-up carefully balances that jagged edge on the edge of the glory hole after blowing, carefully heating up just the part of the glass that needs to be trimmed.
The finisher then selects the right size shears to cut through that thickness of glass. We call our tiniest shears ‘cup shears,’ because they have short, narrow blades that can fit into, and thus cut, the smaller, narrower pieces of glass we make - our bud vases, or tumblers, or mini spires. The larger pieces, which already have a wide lip or opening, use bigger, heavier shears.
Always, when the finisher is cutting the ribbon of glass off of the lip of the piece to smooth it out and bring it down to the right size, they have to be careful to keep turning the pipe so those ribbons fall away from his hand and body.
Shears are also used in other contexts! Our diamond shears – not named that because they’re diamond-coated or -tipped, but because they form a small open diamond between their blades. For wares like pumpkins, which are blown into moulds, the neck of the pumpkin is cut all the way down to the top of the pumpkin. The diamond shears close in the entirety of the neck of the pumpkin and allow the finisher to snip off the extra glass, and close up the pumpkin.
Finishers also use diamond shears to cut the handles and “bits” of glass that are added to other forms, like pitchers or vases. The bit person will bring a piece of hot glass, and the finisher will use their shears to guide that hot glass to where it needs to land on the piece to be shaped into a handle, or a thumb loop, or a decorative blob.
All told, shears do a good deal of hard work for us – snip snip!