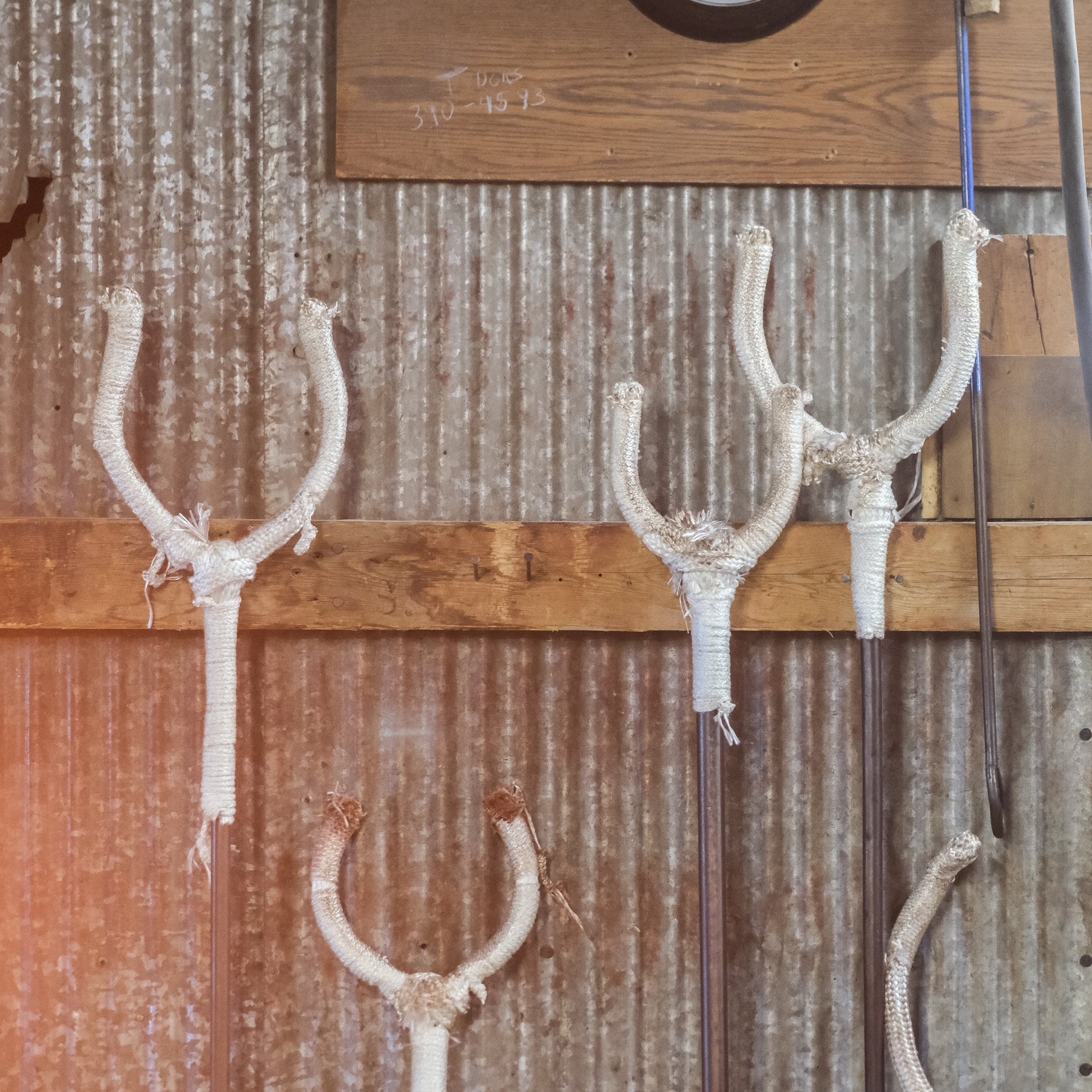
Tools of the Trade Tuesday! - Forks!
Forks – not just for eating anymore! We use a range of differently sized and shaped metal contraptions to carry our super hot glass from the finisher’s bench to the lip of the lehr – because hands won’t suffice! When our glass leaves the bench for the last time, the temperature of the glass is still a steamy 2000 degrees Fahrenheit, and we move too much glass too quickly to don Kevlar suits and gloves and carry each piece by hand to the annealing over.
That’s where the forks come in! Almost all of our forks are made with two metal prongs affixed to the end of a metal pole. These prongs are adjustable – you’ll often see the finisher knocking the forks closer together, or further apart, before they invert the finished piece onto them. Why are there only two prongs? So that the neck of the piece, or the foot of it, can be slid between them and nestled and balanced in.
Our Carry-In person is usually one of our junior apprentices: it’s one of the early skills you learn on the hot shop floor. But it’s certainly not an easy job: it requires strength and balance and measured steps. The Carry In often needs to torch the bottom of the piece to remove the sharpest parts of it, and has to keep that fork, and that piece, balanced carefully so it doesn’t topple over and crash. Larger pieces are even more complicated to manuever with forks – especially pieces that are too tall to fit into the lehr! For our larger glass, the Carry In usually has to lay it on its side, on two other metal prongs, so that it doesn’t scrape the top or topple over.
Our metal forks are wrapped with Kevlar twine, and that, too, is an early task our apprentices learn on the hot shop floor – how to tightly tie and entwine the white heat-proof rope that provides some texture for gripping and a nest to keep the piece from rolling off of the smooth metal.
Forks - like the other tools we use – are prosthetics for our hands, which have to be protected from the tremendous heat of our glass. Tools are what allow us to extend our bodies and get in touch with the material when we can’t touch the material.
