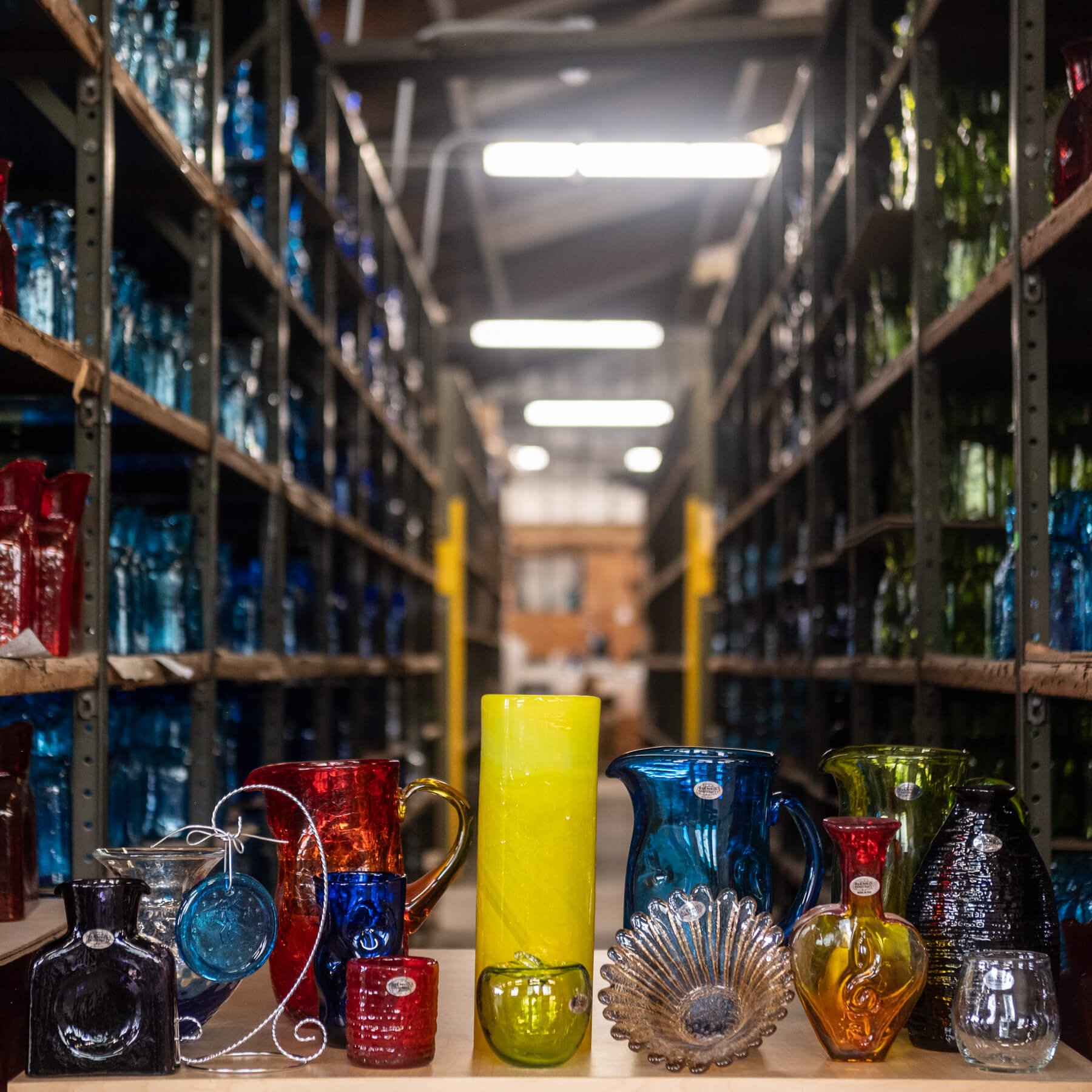
What’s Second Quality Glass?
Timing. Temperature. Sequence.
These are the words that glassmakers everywhere live and die by. The right things in the right place at the right time and the right temperature in the right order. Each of our hot shop teams is 3-8 workers who depend on each other to get all three of those elements locked into place to make the most beautiful glass we can as often as humanly possible.
But, the best laid plans of mice and men are subject to wildly variable conditions, all of the time. The conditions under which our glass is made, maintained, gathered, blown, finished, and annealed are changing every single day. The variables are - to put it mildly - mind-boggling.
Blenko is handmade. Everything about it is profoundly, really, hand made. Our glass is mixed on premises from raw materials just about every day, and fed to furnaces in various stages of living and dying. (The realistic note is that every glass furnace starts to fall apart - literally - the first time it’s used.) We strive for - and achieve - the best quality glass we can given the limitations of our infrastructure. Every piece of hot glass is handled by multiple people, which multiplies the chances that something will go wrong.
Hot glass has a character and will of its own. Our first designer, Winslow Anderson, observed that hot glass is like a willful child – it will do what it wants to do, and it wants to show off. But it can also be sulky and inflexible, stubborn and difficult to work with.
All of our glass bears the marks of our making; glass is a medium that shows everything that’s been done to it. We love this about the handcrafting process, and glass, too, and know this is what sets us apart from machines. We have high expectations for our glass, but sometimes the signs of our craftsmanship show up where we don’t want them. Overall, we judge each individual piece for its whole achievement – there are a lot of considerations in the balance, and it’s as much an art as a science. Does the individual piece achieve what it’s meant to achieve - express what it needs to express?
Included below is a quick-and-dirty guide to the work of Quality Control at Blenko, the better to explain why these beautiful, functional Second Quality pieces fall short of our First Quality standards. None of these quality standards in and of themselves disqualifies a piece from being First Quality, but a Second Quality piece will certainly include one or more of the following complications.
Second Quality Glass, A Glossary
When we consider what is second quality in terms of glass quality, there are a few things we take note of, from glass quality to maker errors.
“Stones” are the small pieces of refractory, or the furnace liner, that appear as small flecks or flakes in the glass, sometimes white, sometimes invisible. Sometimes our batches of colored glass will develop an additional shimmer or mild opalescence when the refractory dissolved evenly into a batch.
Bubbles are just what they sound like - small pockets of air trapped within the glass. “Cords” are the lines you can sometimes see in handmade glass, and are the result of temperature differentials in the glass in the furnace. (Even raging hot furnaces have cold spots!) Like cords, “lap marks” are small waves or wrinkles on the surface of the glass due to inconsistent temperature changes. Our thicker or heavier glass may sometimes bear folds or wrinkles from its gathering.
Other aspects of glass quality are considered for quality. One is the consistency and reliability of color. Sometimes color comes out unpredictably, or off shade. Our colors that change according to temperature - striking colors like Tangerine or Coral - are notoriously difficult to heat and reheat and achieve reliable results. Some of our colors can overstrike, or “smoke,” creating spots or streaks of discoloration. Applying frit to glass adds its own hazards - it can be applied unevenly, or along a finished edge, or cool differentially from the rest of the glass, creating color or effect defects.
Tools leave their own marks on the glass. Shear marks are the traces of where the glass has been cut, either to pour it into a mould, or applied as a bit. Fire polishing can remove these things, but sometimes imperfectly. Our blowpipes sometimes leave small iron inclusions in our glass, which may appear as small black flecks.
The annealing oven is a necessary part of our glass’s journey, but sometimes it can leave a mark - literally. “Chain marks” appear when a piece of hot glass is slid or pushed over the conveyor belt, leaving a trace or mark.
In terms of design, there are even more considerations. Form and finishing are critical in judging quality. If the finished object doesn’t conform to the size, height, or shape of the design, it is judged second quality. If the finishing of the piece - the bit work, or handle, or dimples, or crackle, or spiral, or - or - or! doesn’t meet specifications, it is judged second quality.
Sometimes our blowers don’t have the breath or misjudge - leading to underinflation of the glass in the mould. In our dump molds, sometimes we’re a little overzealous, leading to an overpour. Our moulds sometimes cause us problems, as when they’re incorrectly or poorly closed during the blowing process, leading to seepage or overpronounced seams.
(Whew)
It’s a wonder anything is First Quality at all! But our glass is hand made. It’s what sets us apart from machines and mechanization: that we do our best with our hands to make the best quality glass we can. Our Second Quality glass - well - it’s just more unique, but no less beautiful than our First Quality glass. Personally? I like these pieces best. Nobody’s perfect, and neither is our handmade glass.